Fasteners and Machining: Trick to Effective and Dependable Manufacturing
Fasteners and Machining: Trick to Effective and Dependable Manufacturing
Blog Article
Browsing the Globe of Fasteners and Machining: Techniques for Precision and Speed
In the intricate world of bolts and machining, the pursuit for accuracy and rate is a continuous obstacle that requires careful interest to information and calculated preparation. From recognizing the diverse selection of fastener kinds to selecting optimum products that can withstand rigorous needs, each action in the process plays a critical role in accomplishing the desired outcome. Accuracy machining techniques additionally elevate the intricacy of this craft, requiring a fragile equilibrium in between technical experience and cutting-edge approaches. As we explore the strategies that can improve both rate and performance in this domain, the interplay in between quality control procedures and functional excellence arises as a crucial focal factor.
Understanding Fastener Kind
When choosing fasteners for a task, understanding the various types offered is essential for making sure optimum efficiency and dependability. Fasteners can be found in a vast array of types, each designed for particular applications and demands. Bolts are used with nuts to hold products together, while screws are functional fasteners that can be utilized with or without a nut, depending upon the application. Nuts, on the other hand, are inside threaded fasteners that friend with screws or screws, providing a secure hold. Washing machines are vital for distributing the tons of the bolt and avoiding damage to the material being attached. Furthermore, rivets are permanent bolts that are excellent for applications where disassembly is not needed. Recognizing the differences in between these fastener kinds is essential for selecting the right one for the job, making sure that the link is solid, resilient, and reliable. By selecting the ideal bolt kind, you can enhance the efficiency and long life of your task - Fasteners and Machining.
Choosing the Right Products
Understanding the importance of choosing the ideal products is extremely important in making sure the optimum efficiency and reliability of the picked bolt types talked about formerly. When it concerns fasteners and machining applications, the product selection plays an essential role in establishing the overall stamina, sturdiness, rust resistance, and compatibility with the desired setting. Different products offer differing homes that can substantially impact the performance of the fasteners.
Common products utilized for bolts consist of steel, stainless steel, brass, titanium, and aluminum, each having its special strengths and weak points. Steel is renowned for its high strength and longevity, making it suitable for a wide variety of applications. Stainless steel offers exceptional deterioration resistance, suitable for settings susceptible to moisture and chemicals. Light weight aluminum is corrosion-resistant and light-weight, making it appropriate for applications where weight reduction is essential. Brass is frequently chosen for its aesthetic allure and superb conductivity. Titanium is recognized for its outstanding strength-to-weight proportion, making it excellent for high-performance applications. Choosing the appropriate material involves taking into consideration variables such as toughness demands, ecological conditions, and budget restraints to make certain the desired performance and long life of the bolts.
Precision Machining Techniques
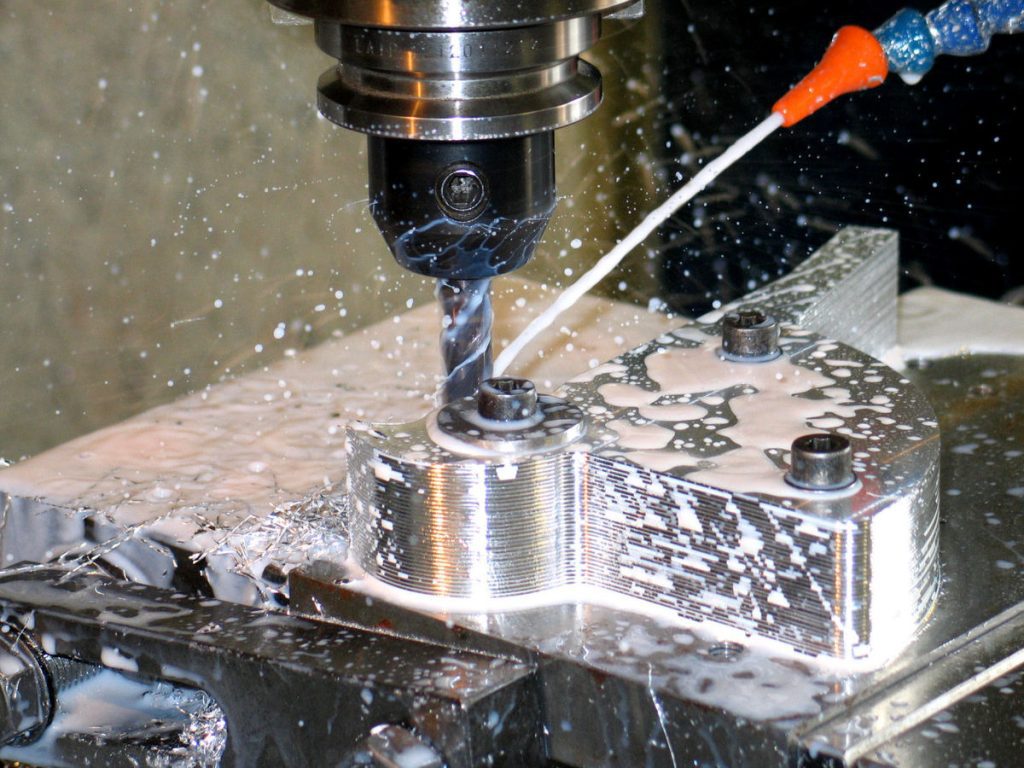
Along with CNC machining, other accuracy techniques like grinding, turning, milling, and drilling play essential functions in bolt production. Grinding helps attain great surface area coatings and limited dimensional tolerances, while turning is usually used to develop round components with accurate sizes. Milling and drilling procedures are crucial for shaping and producing openings in fasteners, guaranteeing they fulfill specific requirements and feature properly.
Enhancing Rate and Performance
To optimize bolt production procedures, it is vital to streamline procedures and implement reliable methods that complement accuracy machining techniques. Automated systems can manage repetitive jobs with accuracy and speed, permitting workers to concentrate on even more facility and value-added activities. By incorporating these methods, producers can achieve a balance in between rate and precision, inevitably improving their competitive side in the bolt industry.
High Quality Control Measures
Executing strenuous quality assurance procedures is crucial in making sure the reliability and consistency of fastener products in the production procedure. Quality control steps incorporate numerous stages, beginning with the choice of basic materials to the last inspection of the completed fasteners. One essential facet of top quality control is home conducting extensive product examinations to validate conformity with specifications. This includes examining variables such as product longevity, make-up, and toughness to guarantee that the fasteners fulfill industry criteria. In addition, keeping track of the machining processes is vital to support dimensional precision and surface finish high quality. Making use of innovative modern technology, such as automatic assessment systems and precision measuring tools, can boost the accuracy and performance of quality assurance procedures.
Regular calibration of devices and machinery is important to maintain uniformity in manufacturing and ensure that fasteners satisfy the required resistances. Executing stringent methods for identifying and dealing with non-conformities or problems is important in stopping substandard items from getting in the marketplace. By establishing an extensive top quality control framework, suppliers can maintain the credibility of their brand and provide bolts that meet the highest possible requirements of efficiency and durability.
Conclusion
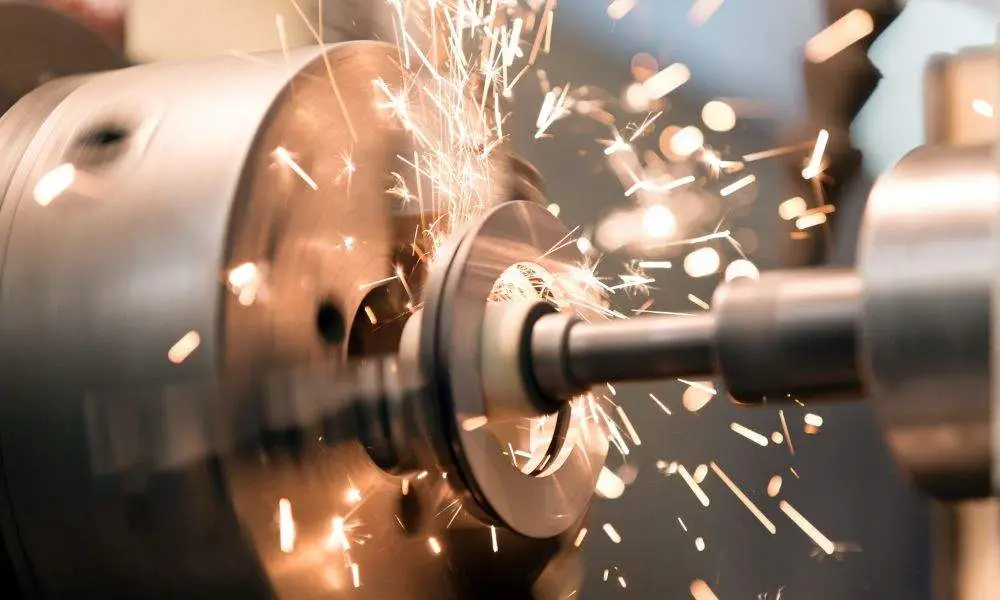
In the elaborate world of bolts and machining, the mission for accuracy and speed is a Recommended Site continuous obstacle that demands precise focus to information and calculated planning. When it comes to fasteners and machining applications, the product choice plays an essential duty in figuring out the overall strength, durability, deterioration resistance, and compatibility with the designated setting. Precision machining entails numerous advanced techniques that make certain the limited resistances and specs needed for fasteners.In addition to CNC machining, various other accuracy strategies like grinding, transforming, milling, and drilling play essential roles in fastener production.To maximize bolt production processes, it is crucial to improve procedures and implement effective approaches that enhance precision machining techniques.
Report this page